TM 5-4220-227-14
Table 5-1. Direct Support Troubleshooting Procedures (Cont).
MALFUNCTION
TEST OR INSPECTION
CORRECTIVE ACTION
3. HEATER/CHILLER FAILS TO FUNCTION.
Step 1. Inspect motor contactor. It may prevent the pump from operation.
Notify General Support Maintenance of faulty contactor.
Step 2. Inspect the 1/3 HP motor. It may be the cause of the pump not operating.
Notify General Support Maintenance of faulty motor.
Step 3. Check Freon level in sight glass. If air bubbles persist longer than one minute, Freon is low.
Notify General Support Maintenance for addition of Freon.
Step 4. Freon level lowers after being replaced.
Notify General Support Maintenance to check for leaks.
Step 5. Check filters. If there is a noticeable temperature difference between input and output lines, filters may
be clogged.
Notify General Support Maintenance to replace filters.
Step 6. Check expansion valve for frost. Internal overload relay may have tripped.
Allow time to reset.
Step 7. Check compressor for frost. Expansion valve may have failed causing fluid not to cool.
Notify General Support Maintenance to replace expansion valve.
Step 8. Check for 220 Vac across condenser for motor contractor. This may cause the condenser fan not to
operate.
a. If voltage is not present, check power cord to source.
b. If voltage is present, notify General Support Maintenance to replace fan motor contactor.
Step 9. Inspect condenser fan motor. Check voltage across connections. Fan will not run if voltage is not
present.
If voltage is present, but motor does not operate, notify Direct Support Maintenance to replace
condenser fan motor.
5-3/(5-4 blank)
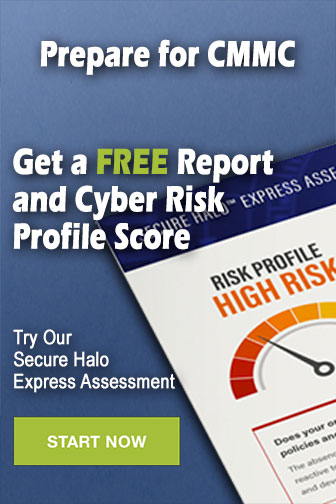