TM 5-4220-227-14
2-8. Reporting Deficiencies. If any problem with the equipment is discovered during PMCS or while it is being
operated that cannot be corrected at the operator/crew maintenance level, it must be reported. Refer to DA Pam 738-
750 and report the deficiency using the proper forms.
2-9. Equipment is Not Ready/Available If Column. This column lists conditions that make the equipment unavailable
for use because it is unable to perform its mission, or because it would represent a safety hazard. Do not accept or
operate equipment with a condition in the "Equipment is Not Ready If" column.
Table 2-1. Operator Preventive Maintenance Checks and Services (PMCS).
NOTE
Within designated intervals, these checks are to be performed in the order listed.
If the equipment must be kept in continuous operation, check and service only those items that can be
checked and serviced without disturbing operation. Make the complete checks and services when the
equipment can be shut down.
B - Before
D - During
A - After
Interval
Item
Item to be Inspected.
Equipment Is Not Ready
No.
B
D
A
Procedure
Available If
1
GFI. Press TEST button. Observe indicator light is
GFI inoperative.
off Press ON button. Observe indicator light is lit.
2
Power Strip. Press circuit breaker switch. Observe
Power strip inoperative.
indicator light is off. Press circuit breaker switch
Observe indicator light is lit.
3
Interior Lights. Check all interior lights for function.
4
Primary Communications System. Check the com-
System damaged or inoperative.
munications for proper function in both the I/L and
Do not operate until repaired.
O/L and without headsets.
5
Secondary Communications System. Check sound
Sound power phone damaged
powered phones for proper function.
or inoperative.
6
Oxygen (02) Analyzer. Check 02 analyzer proper
function.
7
Carbon Dioxide (C02) Scrubber and Chiller Unit.
Check CO2 scrubber and chiller blower units to ensure that
both units are circulating air.
2-12
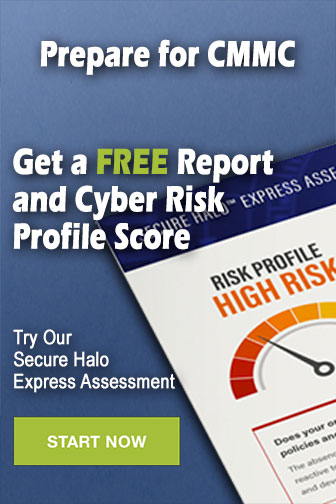