TM 5-4310-384-13
SECTION II. EQUIPMENT DESCRIPTION
1-7.
PURPOSE OF THE AIR COMPRESSOR. An electric motor driven compressor for testing of missile plumbing
systems.
1-8.
CAPABILITIES AND FEATURES.
a.
Two stage compressor provides compressed air at 5 cfm and 175 psi.
b.
Electric motor driven.
c.
Magnetic motor starter with thermal relay protects motor against overload.
d.
Pressure switch provides for automatic compressor cut-in at 160 psi and cut-out at 190 psi.
e.
Tank safety relief valve to prevent damage to compressor and injury to personnel.
f.
Automatic unloading of compressor unit upon machine shutdown.
g.
Air discharge system with regulator/filter and dehydrator.
h.
Tank mounted pressure gage gives constant reading of air pressure in tank.
1-9.
DESCRIPTION OF COMPRESSOR COMPONENTS.
a.
Air Tank (1). A 30 gallon air tank with welded boss openings for check valve, pressure gauge, pressure switch,
shutoff valve, and safety relief valve. Has a welded platform base for electric motor and compressor mounting. Has
welded support brackets for mounting casters.
b.
Check Valve (2). Spring and poppet valve that prevents air from returning to the compressor head from the
tank. Has threaded opening for unloader line fitting.
c.
Aftercooler Tubing (3). Air discharge tubing from high pressure cylinder head to check valve and air tank.
d.
Compressor Unit (4). A two stage air cooled pump driven by pulleys and V-belts. Rated at 5 cfm at 175 psi.
e.
Intercooler Tubing (5). Finned copper tubing between the high and low pressure cylinder heads. Provides heat
dissipation between the high and low pressure cylinder heads.
f.
Electric Motor (6). Single phase, 2 hp induction motor with capacitor. Shaft mounted pulley powers larger
compressor flywheel. Wired in series with pressure switch and magnetic motor starter.
g.
Motor Starter (7). Contacts are magnetically closed when power is applied. Contains a melting relay which.
opens the circuit when a current overload is sensed. Enclosure contains ON/OFF switch (8) and RESET button (9).
h.
Thermostat (10). Factory set; 48" capillary length, probe (bulb) is inserted in heat block bowl assembly of
regulator/filter.
i.
Pressure Switch 11). Controls operating pressure range between 160 psi (cut-in) and 190 psi (cut-out) with a
differential of 30 psi. Diaphragm senses operating pressure and opens and closes contacts. Adjustable pressure setting.
Contains a pressure relief fitting for the unloader line.
j.
Pressure Gage (12). Provides continuous reading of tank pressure between 0-300 psi.
k.
Safety Relief Valve (13). Tank mounted valve with relief setting of 200 psi. Pull ring for manual check of
operation.
I.
Dehydrator (14). Dries air before being discharged through air hose. Mounted on bracket next to
regulator/filter on side of air tank.
m.
Regulator/Filter(15). Regulates and filters air between air tank and dehydrator. Mounted on bracket next to
dehydrator on side of air tank.
n.
Heater Block (16). Prevents freezing of accumulated moisture in low ambient temperature. Controlled by
preset thermostat.
1-3
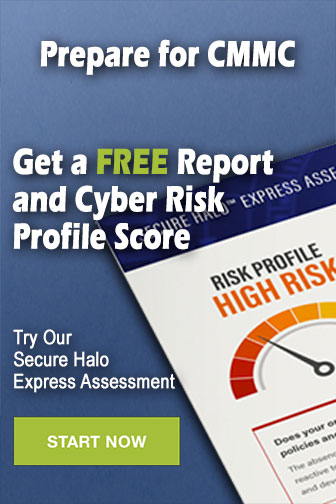