TM 5-4310-387-14
WARNING
The filter adapter and recharge connection should be thoroughly inspected prior to servicing and
any trace of oil, grease, or foreign material carefully removed. Use only those adapters and
connections supplied and designed for this equipment. Secure the dust cap between the
handlescrew and the adapter seat when the filling adapter is not in use.
Never open filling valve when under pressure and not connected, as highly compressed air
emerging can cause serious accidents.
Check air tightness of compressor from time to time by brushing all fittings and couplings with
soapy water to detect air bubbles, indicating an air leak. Repair all air leaks.
Filling hose must always be in satisfactory condition and threads undamaged. Discard worn or
damaged hose.
WARNING
Permit only qualified personnel to use this equipment. Complete familiarity is a basic prerequisite
to safe operation techniques. The operator must always be in attendance when equipment is in
use.
Section III. PRINCIPLES OF OPERATION
Paragraph
Page
1-12
Compressor Air Flow .......................................................................................................
1-6
1-13
Compressor Lubrication System ......................................................................................
1-8
1-14
Detailed Principles of Operation for Engine Assembly .....................................................
1-8
1-12. Compressor Air Flow. (Figure 1-3) Air is taken into the first stage of the compressor by way of the prefilter and
the inlet air filter. The movement of the piston within the first stage cylinder compresses the incoming air to about 70
PSIG (4.8 BAR). The air leaving the first stage is cooled by the first to second stage intercooler. Both the first stage
cylinder and the first to second stage intercooler are protected from overpressure by the first stage safety valve. The
compressed air entering the second stage Is compressed to a pressure of about 550 PSIG (38 BAR). The air leaving the
second stage is cooled by the second to third stage intercooler. The cooled compressed air enters the interstage
separator. Inside the interstage separator, a sintered metal filter removes any solid contaminants from the air. A series
of air directing vanes and baffles cause the air flowing through the separator to spin. The resulting centrifugal force
causes the water vapor and oil vapor which was condensed by the intercooler to collect on the inside surface of the
separator housing and flow down into the sump area at the bottom of the separator. The accumulated condensate may
then be drained by means of the separator drain valve. The second stage cylinder, second to third stage intercooler and
the interstage separator are all protected from overpressure by the second stage safety valve. The compressed air
entering the third stage is compressed to a pressure of about 3260 PSIG (225 BAR). The high pressure air leaving the
third stage is cooled to within about 25°F (14°C) of ambient temperature by the aftercooler. It should be noted that the
interstage coolers and the aftercooler are located directly in the air blast from the compressor cooling fan. The cooled
compressed air
1-6
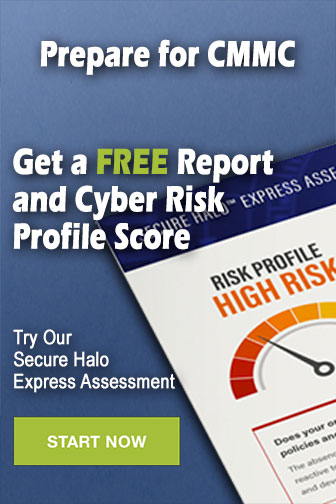