TM-5-4310-389-14
Section III
TECHNICAL PRINCIPLES OF OPERATION
1-11 COMPRESSOR. The compressor is driven at constant speed and, when the final air pressure is reached, the
pressure relief valve opens to the atmosphere. When air pressure is reduced to 4600 psi, the relief valve closes. Each
stage of the compressor is connected to the next higher stage by an intercooler. The fourth stage discharge is connected
to an after cooler. The purpose of the coolers is to reduce the temperature of the compressed air. A separator is
connected to the second, third, and fourth coolers to drain the oil and moisture accumulated during compression and
cooling of the air. The accumulated water and oil vapors should be drained every 15 minutes by depressing the switch
on the instrument panel so all separators drain.
1-12 AIR FLOW. Refer to figures 1-3 and 1-4. The first stage (I) of the compressor draws in atmospheric air through
micronic intake filter (1). Here the air is compressed to a pressure of about 45 psi (3.0 bar). The compressed air
entering the second stage (II) is recooled by the intercooler (2). In the second stage (II), the air is further compressed to
about 230 psi (16 bar), then passed through the intercooler (3) and interfilter (6) to the third stage (III). In the third stage,
the air is compressed 1000 to 1100 psi (70 to 75 bar). Leaving the third stage, the air passes through intercooler (4) and
interfilter (7) to the fourth stage (IV). In the fourth stage, the air is finally compressed to the operating pressure of the
compressor unit. On leaving the fourth stage, the air is passed through the after cooler (5) and is routed via connection A
to the filter system of the compressor unit. The intermediate pressures of the individual stages are monitored by the
intermediate pressure safety valves. Final pressure is monitored by the final pressure safety valve. Condensate can be
manually drained by a switch on the instrument panel. Upon shutdown, the condensate automatically drains.
1-13 PURIFIERS. The compressed air that leaves the final separator is relatively free from oil vapors and condensate.
At this point, the air is not up to diving air purity. As the air passes through the two purification cylinders, the finer oil and
water vapors, taste, odor, and carbon monoxide are removed, thereby producing pure diving air.
1-10
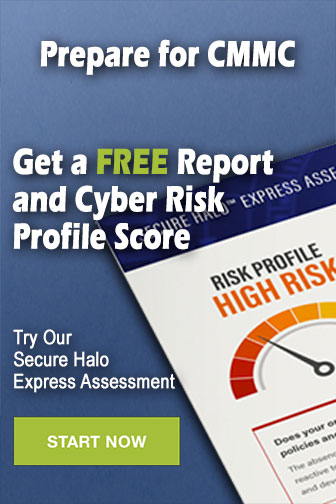