TM 5-4310-379-14
5-11. Fuel Injectors (Cont).
(15) Install check valve (12), check valve cage (13), spring (14), spring seat (15), spring cage (16), needle
valve (17), and spray tip (3) on test adapter and secure with injector nut (2). Install adapter in tester and
perform needle valve tip test. Note the pressure at which the valve opens. The valve should open
between 2200-3300 psi (15,158-22,737 kPa). Repair a fuel injector that does not meet specifications.
(16)
Perform spray tip leakage test. Pressurize fuel injector to 1500 psi (10,335 kPa) and hold for 15 seconds.
Inspect spray tip for leakage. There should be no fuel droplets, although a slight wetting at the spray tip is
permissible.
(17) Perform needle valve lift test using spray tip gage. The lift should be .008-.018 in. (.020-045 cm). If lift is
greater than .018 in. (.045 cm), replace spray tip (3) and needle valve (17). If lift is less than .008 in. (.020
km) check for foreign material between needle valve (17) and spray tip (3).
(18) Perform fuel output test using injector calibrator. The output should be between 57-52 units. If output is
more or less than tolerance, repair fuel injector.
(19) If the fuel injector passes all the above tests, the fuel injector can be reinstalled. Any fuel injector which
fails any of the above tests must be repaired.
b.
Repair.
(1)
Disassemble. (figure 5-6)
(a)
Install injector assembly in injector vise.
NOTE
Discard gaskets and filter. Do not reuse.
(b)
Remove two filter caps (1), gaskets (2) and filter (3).
(c)
Compress follower spring (4) slightly, and raise spring (4) over stop pin (5) and remove stop pin (5).
(d)
Allow spring (4) to rise gradually and remove plunger follower (6), plunger (7), and spring (4) as an
assembly.
(e)
Invert the fixture holding the injector assembly.
(f)
Using injector nut removal tool, remove injector nut (8) and seal (9).
NOTE
If spray tip stays in injector nut, use spray tip removal tool to remove it.
(g)
Remove spray tip (10), needle valve (11), spring cage (12), spring seat (13), valve spring (14), check
valve cage (15), and check valve (16) and place them in a suitable container.
(h)
Remove spill deflector (18) and bushing (19) from injector body (20).
5-20
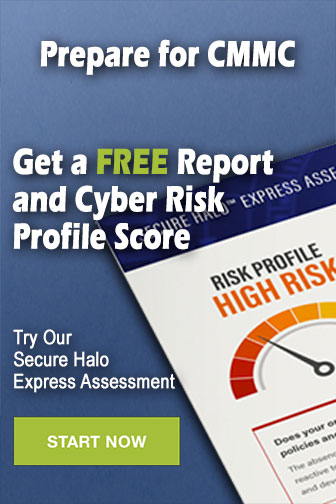