TM 9-4310-397-14
6-6. ROCKER ARMS, CYLINDER HEAD, AND VALVES REPLACEMENT. - Continued
(b)
Slide springs (1), rocker arms (2), and rocker arm supports (3) off rocker arm shaft (4) identifying their
parts for reassembly in the same relationship they were in before disassembly.
b.
Cleaning.
(1)
Scrape all old gasket material from head. Use a powered wire brush to clean sealing surfaces.
CAUTION
Always turn the tool clockwise through the bore, even when pulling back, otherwise tool will
get dull.
(2)
Using special tool (item 6, section III, appendix B), remove carbon deposits from bores for fuel injection
nozzles.
NOTE
Heads with restricted or clogged passages can be cleaned by soaking them in a tank of hot
caustic solution if available.
(3)
If cylinder head is not put in a chemical hot tank for cleaning, clean with solvent (item 11, section II,
appendix E) and a brush. Dry with compressed air and be sure to blow out all passages.
(4)
Wash cam followers, rocker arm parts, push rods, and cap screws with clean solvent (item 11, section II,
appendix E) and dry with compressed air.
(5)
Clean valves.
(a). Hold each valve firmly against a soft wire wheel on a bench grinder.
CAUTION
Any carbon left on the stem will affect alignment in valve refacer if valves need to be refaced.
Do not use wire wheel on plated portion of valve stem.
(b). Make sure all carbon is removed from valve head, face and unplated portion of stem.
(6)
Clean valve guides and seats.
(a). Using a plastic brush, clean valve guides.
NOTE
A few drops of light oil will make cleaning of valve guides easier.
(b). Using an electrical hand drill with wire cleaning brush, remove all carbon deposits from valve seats.
c.
Inspection.
(1)
Check cylinder head for flatness using a precision straight edge and feeler gauge. Check lengthwise and
crosswise in several places. A good secondary check is one that is on a diagonal. The out-of-flat
measurement must not exceed 0.004 in. (0.102 mm) for any one measurement. If any measurement
exceeds this specification, the cylinder head must be either reconditioned or replaced.
6-24
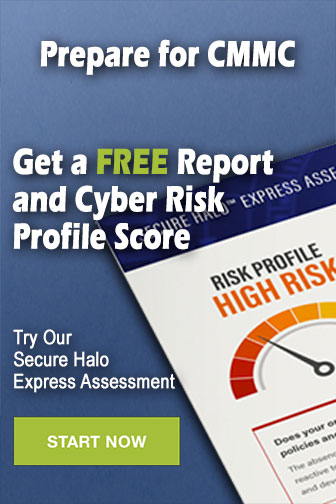