TM 5-4310-379-14
e. Cooling System. The cooling system consists of a radiator, fan, centrifugal-type water pump, and thermostat.
The water pump directs a flow coolant circulating through the engine. Engine coolant is drawn from the bottom of the
radiator core by the water pump and is forced through the oil cooler and into the water manifold and thermostat housing.
From the thermostat housing, the coolant returns to the radiator where it passes down a series of tubes and is cooled by
the air stream created by the fan. When starting a cold engine, or when the coolant is below operating temperature, the
coolant is restricted at the thermostat housing and a bypass provides water circulation within the engine during the warm-
up period.
f. Exhaust System. The exhaust system consists of a unitized muffler and exhaust pipe, designed to decrease the
noise of combustion and to carry the combustion gases up and away from the air intake area. The exhaust pipe is
covered with a hinged, spring-loaded cap to exclude rain. The muffler is threaded for insertion into the engine manifold.
g. Lubrication System. The lubrication system provides lubrication to all moving parts within the engine. A gear-
type pump draws oil from the oil pan, through an intake screen. The oil is then pumped through the oil cooler. After
leaving the oil cooler the flow is divided. A portion of the oil flow is directed to crankshaft front main and connecting rod
bearings, front camshaft and balance shaft bearings, through the oil filter and back to oil pan, and the remainder travels
to cylinder head where it supplies lubrication to valve operation mechanisms, center and rear camshaft, balance shaft,
main, and connecting rod bearings. Oil draining back down from cylinder head also provides lubrication to front and rear
blower bearings and gear train. An oil by-pass valve allows excess oil to by-pass the oil cooler during warm up periods
and in the event the oil cooler becomes stopped up.
1-13.
Detailed Principles of Operation, Air Compressor.
a. Compressor Pulley. The pulley is mounted at front of compressor unit. It is connected to the end of the
crankshaft and held in place with a keyway and two bolts. The pulley provides a means of receiving power from a diesel
engine through a belt arrangement. The rotation of the pulley turns the crankshaft of the compressor to develop
compressed air.
b. Air System. Figure 1illustrates the compressor air system. Air at atmospheric pressure is drawn into the low
pressure cylinder by having the intake valve open on the down-stroke of the piston. On the compression stroke of the
first stage piston, air is forced through the first stage discharge valve and into the high pressure cylinder. The
compressed air from the first stage enters the second stage through an intake valve and is drawn in by the down-stroke
of the second stage piston. On the compression stroke the air is compressed to its final stage and then leaves the high
pressure cylinder by the open discharge valve. The compressed air leaves the compressor through the discharge
manifold. In the event the air supplied by the compressor is greater than the demand, a variable differential pilot valve in
the system will route excess air to the air unloader valves. The air unloader valves receive the excess air pressure on a
diaphragm which drives a pin which in turn opens the intake valves. This action prevents the intake valves from closing
and thereby does not allow compression of air. When the air demand becomes greater than the supply, the variable
differential pilot valve will shut off the air supply to the air unloaders which will in turn allow the intake valves to close,
and the compressor to load.
c. Interstage Safety Valve. The compressor is equipped with two safety valves which are installed in each cylinder
head. The valve will relieve pressure at 100 psi in the event of an obstruction blockage in the passages of the head,
between the high and low pressure stages.
Change 1
1-9
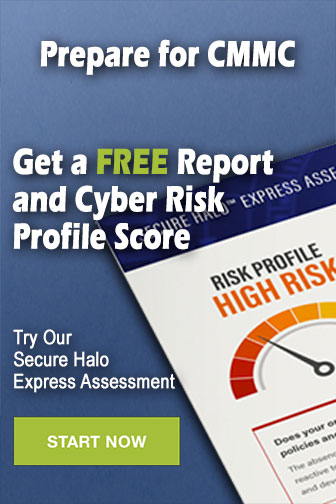