TM 5-4310-379-14
1-12.
Detailed Principles of Operation, Diesel Engine.
a. Starting System. The starting system for the diesel engine is comprised of two 12-volt lead-acid storage
batteries, a starting motor, starter switch, voltage regulator and alternator. In starting the engine, the starter switch is
depressed, battery current energizes the starter motor, which causes the armature to turn. Cranking torque is transmitted
by a Sprag clutch from the starting motor armature to the engine flywheel gear. The Sprag clutch will keep the starter
pinion in mesh with the flywheel until starting is assured or the start circuit is interrupted. When the diesel engine is
running, a belt arrangement drives the alternator which has an electrical output that maintains the battery. The regulator
regulates the voltage and current output of the alternator and maintains the battery in a fully charged condition.
b. Diesel Engine. In the diesel engine, air alone is compressed in the cylinder; after the air has been compressed, a
charge of fuel is sprayed into the cylinder and ignition is accomplished by the heat of compression. A blower is provided
to force air into the cylinders for expelling the exhaust gases and to supply the cylinders with fresh air for combustion.
The cylinder wall contains a row of ports which are above the piston when it is at the bottom of its stroke. These ports
admit the air from the blower into the cylinder as soon as the rim of the piston uncovers the ports. The unidirectional flow
of air toward the exhaust valves produces a scavenging effect, leaving the cylinders full of clean air when the piston
again covers the inlet ports. As the piston continues on the upward stroke, the exhaust valves close and the charge of
fresh air is subjected to compression. Shortly before the piston reaches its highest position, the required amount of fuel
is sprayed into the combustion chamber by the fuel injector. The intense heat generated during the high compression of
the air ignites the fine fuel spray immediately. The combustion continues until the injected fuel has been burned. The
resulting pressure forces the piston downward on its power stroke. The exhaust valves are again opened when the piston
is about halfway down, allowing the burned gases to escape into the exhaust manifold. Shortly thereafter, the downward
moving piston uncovers the inlet ports and the cylinder is again swept with clean scavenging air. This entire combustion
cycle is completed in each cylinder for each revolution of the crankshaft, or, in other words, in two strokes; hence, it is a
"two-stroke cycle."
c. Fuel System. The fuel system, schematically illustrated in Figure 1-4, is comprised of a 30-gallon fuel tank,
injectors, pipes, manifolds, pump, strainer, filter, and connecting fuel lines. When the engine is started by the starting
motor, fuel is drawn from the fuel tank through the strainer by a gear driven fuel pump. The fuel then enters the fuel
pump. Upon leaving the pump under pressure, fuel is forced through the filter and into the inlet manifold in the cylinder
head, where it passes through pipes into the injectors. The fuel is filtered through elements in the injectors and atomized
through small spray tip orifices into the combustion chamber. Excess fuel from the injectors returns through the fuel
outlet manifold and connecting fuel lines to the fuel tank. Since the fuel is constantly circulating through the injectors, it
serves to cool the injectors and to carry off any air in the fuel system.
d. Air System. Air enters the engine through an oil bath air cleaner, which is designed to remove foreign matter
from the air and pass the required volume of air for proper combustion and scavenging. In the intake system illustrated
in Figure 1-5, a charge of air is forced into the cylinders by the blower and thoroughly sweeps out all of the burned gases
through the exhaust valve ports. This air also helps to cool the internal engine parts, particularly the exhaust valves. At
the beginning of the compression stroke, each cylinder is filled with fresh clean air which provides for efficient
combustion. The air, entering the blower from the air cleaner, is picked up by the lower rotor lobes and carried to the
discharge side of the blower. The continuous discharge of fresh air from the blower enters the air chamber of the
cylinder block and sweeps through the intake ports of the cylinder liners. The angle of the ports in the cylinder liner
creates a uniform swirling motion to the intake air as it enters the cylinder. This motion persists throughout the
compression stroke and facilitates scavenging and combustion.
1-7
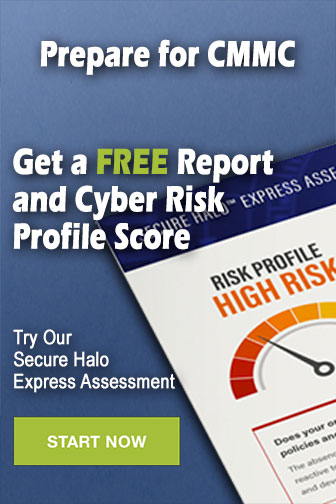