TM 5-4310-379-14
Table 2-1. Operator Preventive Maintenance Checks and Services (PMCS) (Cont).
B - Before
D - During
A - After
W - Weekly
Interval
Item
Item To Be Inspected
Equipment is not
No.
B
D
A
W
Procedure
Ready/ Available if:
6
Check compressor oil pressure - maintain
approximately 17 psi.
7
Gages. Inspect for damaged pointers,
Gages damaged or
cracked lenses, liquid fill leaks, loose tube
inoperative. Do not
connections or loose wires, loose wires,
operate until repaired.
loose hardware, plus proper operation
and normal readings during operation.
8
*
Switches, controls and valves. Inspect for
Switches damaged or
proper operation. Check for looseness,
inoperative.
damage and missing parts.
WARNING
Examine hoses before pressurizing.
Worn or frayed hose may explode.
9
·
Air hose and fittings. Inspect for wear,
Air hose fittings damaged
cracks, cuts, fraying, leaks and loose
Do not operate with
connections.
damaged hose or fittings.
10
·
Check the compressor air distribution
system for air leaks.
11
Open drain valves on air receiver (30 gal.)
and portable air receiver (60 gal.) while in
use momentarily to expel condensation/
water from tanks every 15 minutes.
Section III. OPERATION UNDER USUAL CONDITIONS
Paragraph
Page
2-11
General ...................................................................................................................... 2-8
2-12
Starting Procedures .................................................................................................... 2-9
2-13
Stopping Procedures ................................................................................................ 2-13
2-11. General. The Diving Air Compressor must be located in a well ventilated area to allow sufficient clearance in
order to prevent overheating of the diesel engine. Whenever possible, the radiator side of the diesel engine should be
pointed leeward, to minimize the possibility of exhaust gases entering the air intake on the air compressor.
2-8 Change 1
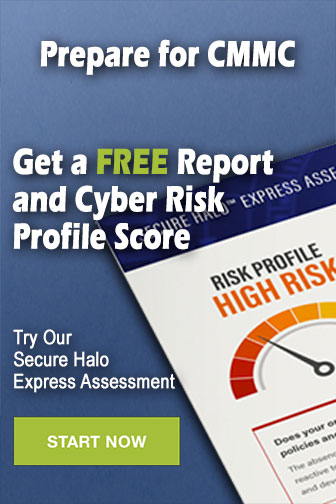