3. Lubrication Instructions For Air Compressor (Model 3LE6A). It is recommended that the oils listed in the
lubrication chart in the front of this manual be used when available. If these oils are not available, any good quality
mineral motor oil (not multigrade) with a viscosity grade of SAE 10W20 may be used if it meets the requirements of the
American Petroleum Institute classification code SE-CC or SE-CD, military specification MIL-L-46152 or HIL-L-2104C.
The crankcase oil capacity of the air compressor model number 3LE6A is 0.50 gallons.
NOTE
The crankcase is connected to the air intake silencer or suction line through a breather valve. Faulty
operation of this valve or clogging of the metered hole will result in too high a crankcase pressure and
promote oil consumption.
4. Troubleshooting The Air Compressor (Model 3LE6A).
Condition
Possible faults
Suggested remedy
1. Insufficient air pressure
a. Air leak(s)
a. Check and correct as necessary
b. Air filter choked
b. Service filter
c. Air pressure switch incorrectly set
c. Adjust switch
d. Air consumption exceeds capacity of
d. Check equipment connected.
compressor
e. Damaged valve(s)
e. Inspect valves and replace
parts where necessary.
f. Pressure gauge defective
f. Check and replace if
necessary
g. Release valve of air pressure switch
g. Check mechanism of valve.
not airtight during loading periods
If leak cannot be cured,
replace valve.
2. Unit does not speed up
a. Low voltage at motor terminals
a. Check generator output.
Adjust if necessary
b. Ambient temperature too low
b. Increase temperature in room
c. Pressure release valve of air pressure
c. Check operation of valve;
switch malfunctioning
replace if necessary
3. Air receiver pressure rises
a. Air pressure switch incorrectly set
a. Set switch to unload com-
above maximum and causes
or out of order
pressor at rated maximum
safety valve to blow
pressure.
Replace switch if
it does not respond
4. Receiver does not hold
a. Non-return valve leaks
a. Check for broken valve and
pressure
springs
b. Air leak(s)
b. Check and correct as necessary
5 Too frequent starting
a. Air pressure switch incorrectly set
a. Increase pressure difference
and too short operating
b. Non-return valve leaks
b. See 4a
periods
c. High condensate level in receiver
c. Drain condensate more
frequently
6 High oil consumption
a. Oil level too high
a. Do not overfill crankcase.
Keep level within lower half
of sightglass
b. Breather valve malfunctioning
b. Replace breather valve
c. Piston ring(s) worn or broken
c. Have condition of piston rings
checked
7. Loading periods too long
a. Excessive air consumption
a. Decrease consumption
b. Compressor not in optimum condition
b. Have compressor inspected
c. Sticking or damaged valves
c. Clean or replace
8. Unit does not start
a. Electrical failure
a. Check or have electrical
system checked
b. Air pressure between stopping and
b. Wait until air pressure is
starting pressure setting
lower than pre-set starting
pressure of air pressure
switch
c. Coupling sleeve damaged
c. New sleeve
2A
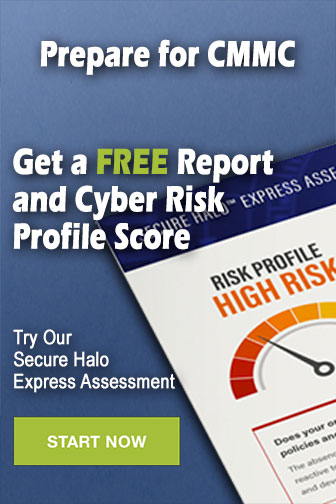