TM 5-4310-385-13
g.
Turn crankshaft (5) until high pressure piston (11 ) is at TDC and repeat above steps i and j.
h.
Remove capscrews (12) securing breather chamber cover (13). Remove cover.
i.
Discard cover gasket (14).
j.
Remove felt oil separator (15) and breather element (16).
k.
Remove crankcase cover (17).
I.
Remove and discard crankcase cover gaskets (18) used as shims.
m.
Remove crankshaft (5) with bearings (19) and cups (20) in place. Leave bearings on crankshaft until after
inspection.
n.
Remove oil drain cap (21), elbow (23), and pipe nipple (22).
o.
Remove opposite drain plug (24) and both filler plugs (25).
p.
Remove oil seal (26) by driving out from inside of crankcase and discard.
q.
Do not remove oil level gage (27) unless broken or unreadable. Gage is press fit into crankcase and removal
by driving out will damage it.
INSPECTION.
a.
Inspect cylinder (2) for cracks, broken cooling fins, and scored cylinder. Replace as necessary.
b.
Inspect pistons (6 and 11) for cracks, broken ring seats, or scored surfaces. Replace as necessary.
NOTE
Piston rings should not be reused as they will not seat themselves in the cylinder
bore in the same position as they originally were in.
c.
Inspect piston rings for any signs of wear. New piston rings should normally be installed during cylinder
assembly.
d.
Inspect connecting rods (10) for scored bearing surfaces and loose fit. Replace as necessary.
CAUTION
Crankshaft bearings and bearing cups are matched sets. If bearing replacement is
necessary, replace both bearing and cup.
e.
Inspect crankshaft (5), bearings (19), and cups (20) for scored journals or pitted bearings. Replace as necessary.
Refer to paragraph 4-9.
f.
Inspect crankcase (3) for cracks or warpage. Inspect all pipe plug threads for damage. Retap threads or replace
crankcase as necessary.
g.
Inspect oil level gage (27) for cracked glass or unreadable scale. Replace as necessary.
4-5
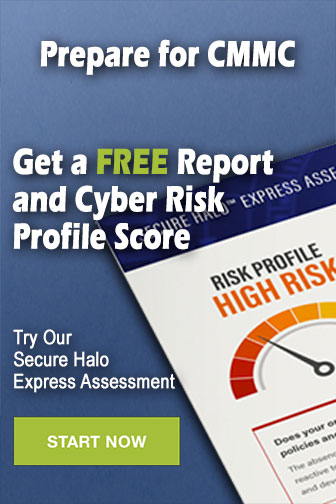