TM 5-4310-385-13
b.
Remove electric motor from air tank base. Refer to paragraph 3-33.
NOTE
Before beginning disassembly, slowly rotate motor shaft by hand to check out
bearings. If you notice any rough spots or binding, bearings are bad and must be
replaced. Bearings are sealed and cannot be visually inspected.
c.Remove four thru bolts (1) and nuts (2).
d.
Mark endplates (3, 8) and remove front endplate (3).
e.
Remove rotor assembly (4).
f.
Remove bearing guards (5), if present. (Guards are used as shims for adjusting shaft end play.)
g.
Using a suitable bearing puller, remove bearings (6) if any binding or rough spots were noticed prior to
disassembly.
h.
Remove cooling fan (7).
i.
Remove rear endplate (8).
j.
Remove thrust washer (9).
k.
Remove screws (10) from conduit box lid (11).
INSPECTION.
a.
Inspect leads and windings (14) of stator assembly (15) for evidence of cracked or burned insulation.
Replace if leads or windings are damaged.
b.
Inspect rotor and shaft assembly (4) for loose or damaged fan. If damaged, replace motor.
c.
Remove any small nicks on keyway with file.
d.
Inspect bearings (6) for wear or loose roller cone. Replace as necessary.
e.
Inspect endplates (3 and 8) for cracks or plugged vent slots.
f.
Inspect bearing guards (5) and thrust washer (9) for cracks or bends. Replace as necessary.
CLEANING.
WARNING
Clean motor components with compressed air no greater than 30 psi. Eye
protective wear must be worn when cleaning with compressed air or scraping
paint.
a.
Remove any loose paint from frame.
b.
Blow off stator and rotor assemblies (4 and 1 5) with compressed air. Wipe rotor assembly (4) with clean rag.
c.
Wipe off bearings (6) with clean rag if grease is dry or dirty. Apply a coat of new bearing grease.
d.
Clean endplate (3 and 8) vent slots with compressed air and wipe off with clean rag.
4-12
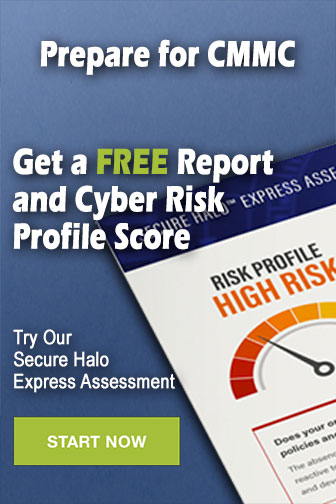