TM 5 4310-451-14
4-41. ENGINE CONTROL ASSEMBLY ADJUSTMENT (Cont).
5.
Check that inlet valve (7) is in fully open position, approximately 15°-20° off vertical center of shaft.
NOTE
Ensure all service valves are closed before starting engine.
6. Start engine (see paragraph 2-10) and allow it to reach normal operating temperature.
7. Run engine until air pressure gage reads 95-100 psi (655-690 kPa).
8. Check that connecting link (12) is resting against stop screw (11).
NOTE
If connecting link Is not resting against stop screw, perform steps 9 through 11; if connecting link
is resting against stop screw, perform step 12.
9. Loosen nut (9) on pressure regulator (10) and turn adjusting knob (8) slightly clockwise until 100 psi (690 kPa)
reading is reached.
10. Once pressure reading is reached, turn adjusting knob (8) counterclockwise until connecting link (12) moves
slightly off stop screw (11).
11. Tighten nut (9).
12. Check that engine speed reads 2375-2475 rpm.
NOTE
If rpm reading is below 2375, perform step 13. If rpm reading Is above 2475, perform step 14.
If rpm reading Is within range, perform step 15.
Pressure will Increase or decrease as step 13 or 14 Is performed. Check pressure reading after
each adjustment.
13.
Open service valve to hold pressure at 90 psi (621 kPa) and turn stop screw (11) on engine control rod (2)
clockwise to raise engine speed. Tighten nuts (1 and 3).
14.
Open service valve to hold pressure at 90 psi (621 kPa) and turn stop screw (11) on engine control rod (2)
counterclockwise to lower engine speed. Tighten nuts (1 and 3).
15.
Close service valve until speed of 1150-1250 rpm is stable with service valve fully closed.
16.
Check that pressure reads 110-125 psi (758-862 kPa). If pressure reads within range, adjustment is complete. If
pressure reading is lower or higher, perform step 17.
17.
Reset pressure regulator (10) and adjust compressor control rod (5) until idle speed reads 1150-1250 rpm.
18.
Tighten four nuts (1, 3, 4, and 6).
4-73/(4-74 Blank)
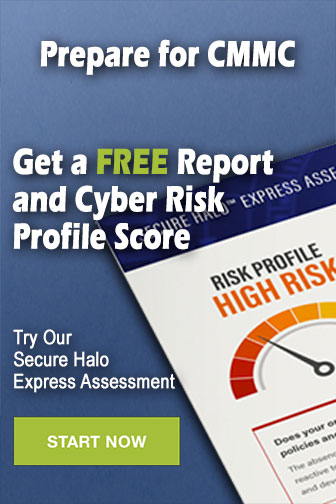