TM 5-4310-451-14
5-55. ENGINE COMPRESSION CHECK.
This Task Covers: Compression Check
Initial Setup
Equipment Conditions:
Tools/Test Equipment:
Engine at normal operating temperature (see para-
General mechanic's tool kit
graph 2-10).
Field automotive shop set
Fuel injector removed (see paragraph 5-57).
COMPRESSION CHECK
1.
Install adapter and compression pressure gage (4) to top of cylinder head (5).
2.
Install jumper connection (2) between fuel inlet (3) and fuel return manifold (1).
CAUTION
DO NOT crank engine with engine starter to obtain compression. Engine must be
running. Failure to follow this caution may result in damage to engine.
3.
Start engine (see paragraph 2-10) and run at 600 rpm.
4.
Observe and record compression pressure indicated on compression pressure gage.
5.
Perform steps 1 through 4 for each of six cylinders.
6.
Depending on elevation at which compression check is performed, compression pressures are as follows:
(a)
At sea level, compression pressure must not be less than 425 psi (2930 kPa).
(b)
At 2500 ft (763 m), compression pressure must not be less than 395 psi (2724 kPa).
(c)
At 5000 ft (1525 m), compression pressure must not be less than 364 psi (2510 kPa).
(d)
At 7500 ft (2288 m), compression pressure must not be less than 340 psi (2344 kPa).
(e)
At 10, 000 ft (3050 m), compression pressure must not be less than 315 psi (2172 kPa).
7.
Pressure variation between any two cylinders must not exceed 25 psi (172 kPa).
8.
Stop engine (see paragraph 2-12).
9.
Remove jumper connection (2) between fuel inlet (3) and fuel return manifold (1).
10.
Remove compression pressure gage (4) and adapter from top of cylinder head (5).
5-178
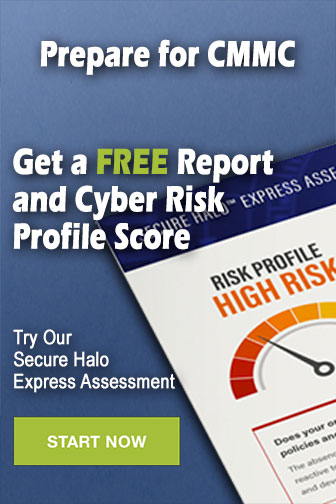